10/23/2023 | Wet Scrubbers | 9 MINUTE READ
Ammonia Scrubbers: Effective Solutions for Emission Control
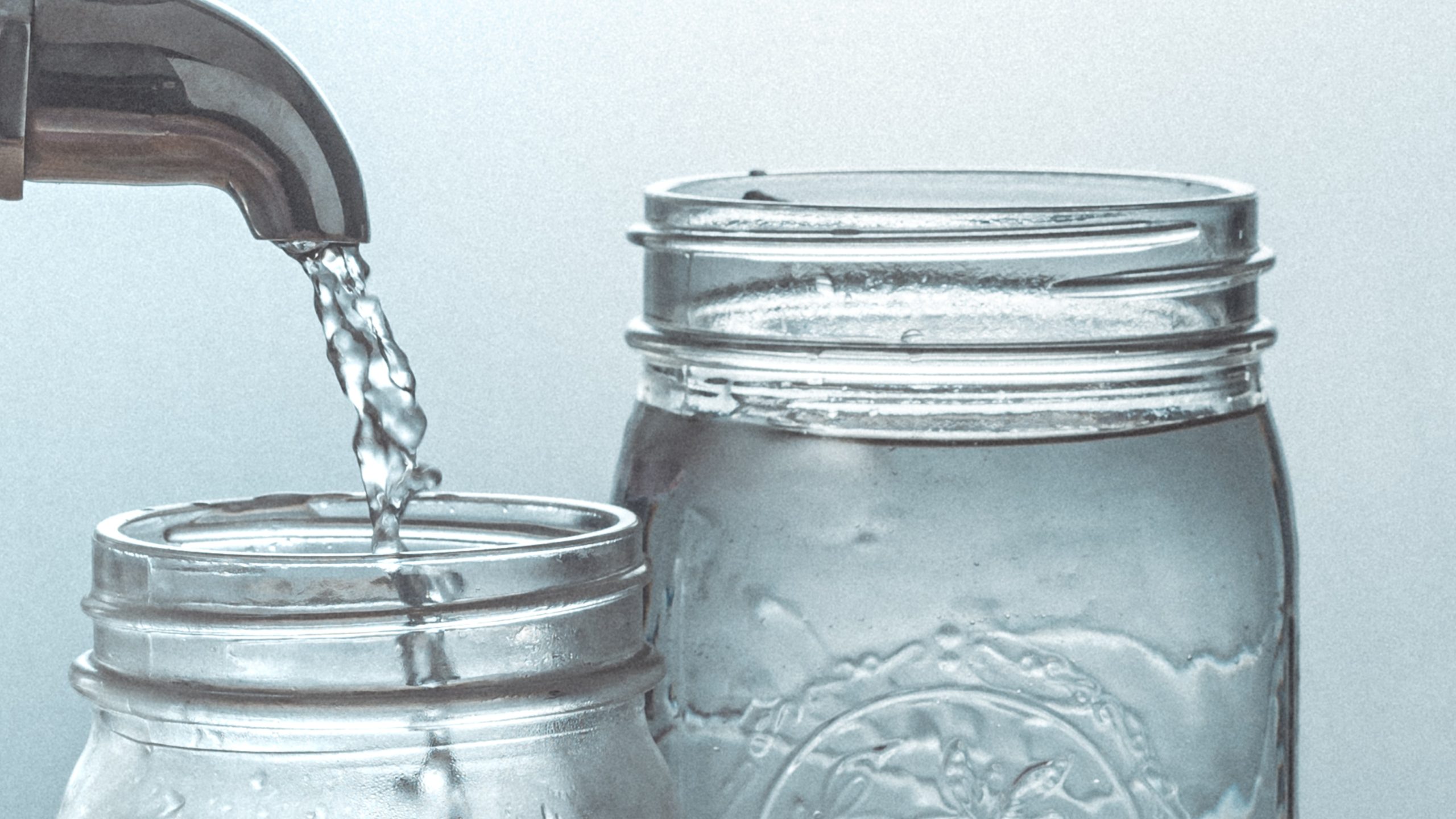
Ammonia, a colorless gas composed of nitrogen and hydrogen, is a common byproduct of various industrial manufacturing processes. While it naturally occurs in air, soil, and water, its presence in high concentrations can pose significant health and environmental risks. Ammonia is toxic when inhaled in large quantities and irritates the eyes, nose, and throat when exposed in lesser amounts. Moreover, ammonia can become explosive when mixed with air under specific conditions, making safety considerations paramount in industries processing high volumes of this gas. Ammonia scrubbers have become increasingly vital to address these challenges and ensure compliance with environmental regulations.

How Ammonia Scrubbers Work
Ammonia scrubbers operate on the principle of chemical reactions to remove ammonia from exhaust streams. Unlike particulate scrubbers that inject liquid into the gas stream, ammonia scrubbers use aqueous acid solutions to neutralize the ammonia. Sulfuric and phosphoric acids are commonly employed due to their low vapor pressures. When these acids react with ammonia, they form salts, effectively removing ammonia from the gas stream. Nitric acid can also be used, generating a potentially usable product for agricultural purposes.
Scrubbing Ammonia vs. Amines
While ammonia scrubbing is a well-established process, scrubbing amines, which are compounds containing nitrogen, can be more challenging. The effectiveness of amine scrubbing depends on factors such as solubility in water and reactivity with acid. Different amines may require distinct approaches or conditions for successful scrubbing, making it essential to consider the specific characteristics of the amine being removed.
Applications and Industries
Numerous manufacturing processes emit ammonia, necessitating the use of ammonia scrubbers. These processes include battery testing, fertilizer manufacturing, digestate dewatering, medical and space-grade silicone production, and refrigeration facilities. In these industries, ammonia is often produced as a byproduct, highlighting the importance of ammonia scrubbers in emission control and environmental compliance.
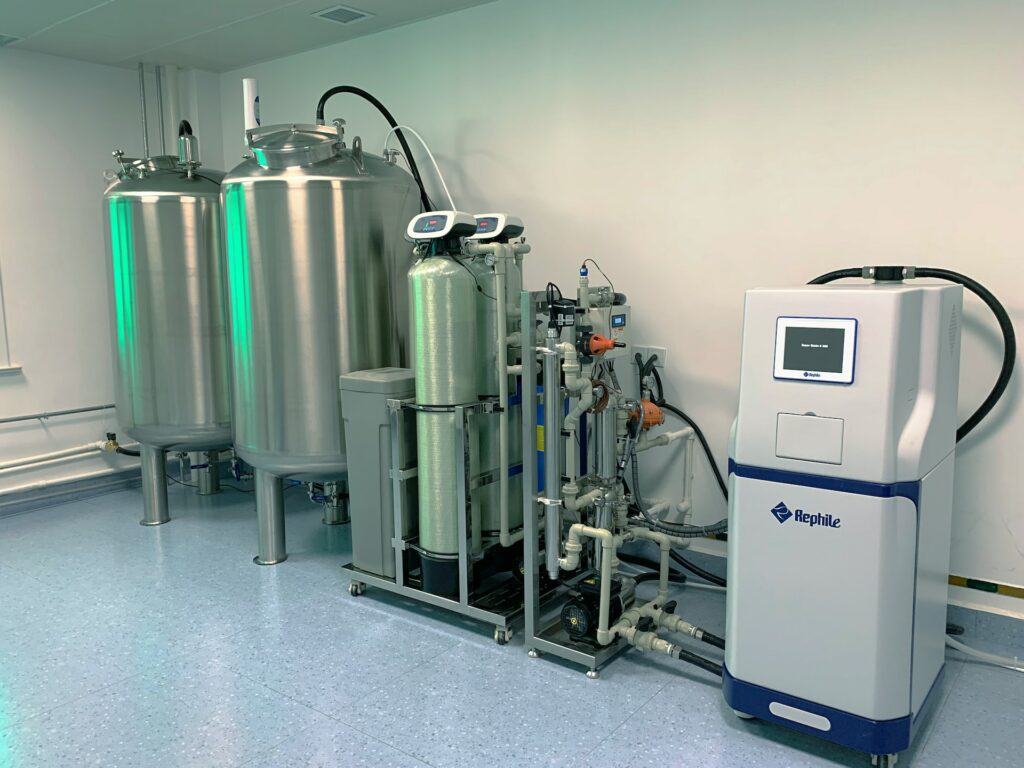
Enhancing Industrial Operations with Ammonia Scrubbers: A Comprehensive Overview of Benefits
The integration of ammonia scrubbers into industrial processes brings forth a multitude of advantages that enhance operational efficiency, minimize environmental impact, and optimize resource utilization. These benefits encompass:
- Unwavering Environmental Compliance: Ammonia scrubbers serve as steadfast guardians of environmental stewardship, enabling industries to adhere to stringent emission regulations. By effectively capturing and removing ammonia from gas streams, these systems ensure that emissions levels remain well within established limits, fostering a harmonious coexistence between industrial activities and environmental sustainability.
- Safeguarding Downstream Equipment: Ammonia, with its inherent reactivity, poses a significant threat to downstream equipment, potentially forming ammonium salts that lead to blockages and corrosion. Ammonia scrubbers act as vigilant protectors, intercepting and neutralizing ammonia before it wreaks havoc on downstream components. This proactive approach safeguards equipment integrity, minimizing disruptions and ensuring seamless operations.
- Embracing Cost-Effectiveness: Ammonia scrubbers emerge as champions of cost-efficiency, offering long-term savings by preventing costly equipment failures and downtime. By eradicating the formation of corrosive ammonium salts, these systems eliminate the need for frequent maintenance and repairs, thereby reducing operational expenses and maximizing profitability.
- Enhanced Efficiency and Productivity: The seamless operation of downstream equipment, facilitated by ammonia scrubbers, translates into enhanced efficiency and productivity. Unimpeded gas flow and the absence of equipment malfunctions ensure that industrial processes run smoothly, minimizing downtime and maximizing output.
- Promoting Sustainability: Ammonia scrubbers play a pivotal role in promoting sustainable industrial practices. By reducing ammonia emissions, they contribute to improved air quality, safeguarding human health and preserving the delicate balance of ecosystems. This commitment to environmental responsibility positions industries as responsible stewards of the planet.
Selecting the Right Ammonia Scrubber: A Comprehensive Guide to Optimized Emission Control
Navigating the intricacies of ammonia scrubber selection is paramount for achieving efficient emission control. To ensure that the chosen scrubber seamlessly integrates into the industrial process and delivers optimal performance, a comprehensive assessment of several key factors is essential:
- System Compatibility: The compatibility of the ammonia scrubber with the gas stream characteristics is crucial for effective emission control. Factors such as gas flow rate, temperature, and pressure must align with the scrubber’s design specifications to ensure optimal ammonia removal efficiency.
- Efficiency: The efficiency of the ammonia scrubber, expressed as the percentage of ammonia removed from the gas stream, is a critical parameter. Scrubbets with high efficiency ratings are favored to minimize emissions and maximize environmental compliance.
- Choice of Scrubbing Media:
- The selection of the appropriate scrubbing media plays a pivotal role in ammonia removal. Commonly employed scrubbing media include sulfuric acid, phosphoric acid, and nitric acid. Each media offers unique advantages and disadvantages, necessitating careful consideration of the specific application requirements.
- Materials of Construction: The materials used in the scrubber’s construction must exhibit exceptional resistance to corrosion and erosion caused by the interaction with ammonia and scrubbing media. Stainless steel, fiberglass, and polyvinyl chloride (PVC) are frequently employed materials due to their durability and compatibility with the scrubber’s operating environment.
- Maintenance Requirements: Regular maintenance is essential to ensure the longevity and performance of the ammonia scrubber. Factors such as the ease of access for maintenance and the availability of replacement parts should be considered to minimize downtime and maximize operational efficiency.
- Cost-Effectiveness: While initial investment costs are important, the overall cost-effectiveness of the ammonia scrubber must be evaluated over its lifespan. Factors such as operating costs, maintenance expenses, and potential downtime should be considered to make an informed decision.
- Regulatory Compliance: The ammonia scrubber must adhere to all applicable environmental regulations and industry standards. This ensures that the system operates within permissible emission limits and minimizes the risk of regulatory penalties.
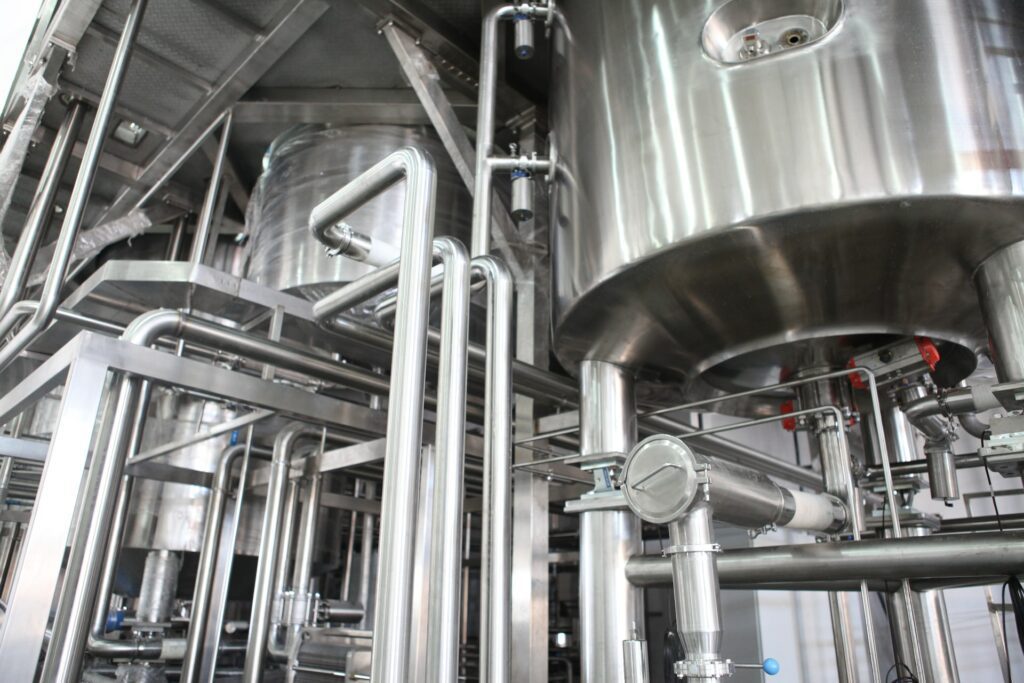
Maintaining Ammonia Scrubbers: A Comprehensive Guide to Media Replacement and System Optimization
Ammonia scrubbers play a vital role in industrial processes by effectively removing ammonia from gas streams, ensuring environmental compliance and protecting downstream equipment. To maintain the effectiveness of these scrubbers, regular maintenance is essential, including the periodic replacement of the scrubbing media. This guide provides a comprehensive overview of the media replacement process, along with insights into maintaining optimal scrubber performance.
Media Replacement Procedure
- Power Disconnection and Heater Blanket Removal: Before commencing the media replacement process, ensure the scrubber is unplugged from any power source. If the scrubber is heated, carefully remove the heater blanket to provide access to the housing.
- Thumbscrew Removal and Yoke Rotation: Locate the thumbscrew on the bottom of the scrubber housing and unscrew it using a suitable tool. Once the thumbscrew is removed, rotate the yoke, which holds the housing together, to allow for easy separation of the housing components.
- Old Media Removal and Disposal: With the housing open, carefully remove the old scrubbing media. Dispose of the used media in an environmentally responsible manner, adhering to local regulations and guidelines.
- Housing Cleaning: To ensure optimal performance, thoroughly rinse the interior of the housing with soapy water. This removes any residual contaminants or debris that could affect the effectiveness of the new media.
- Media Filling: Fill the housing with the recommended amounts of parts A (ceramic burl saddles) and B (white pellets) materials. Follow the manufacturer’s instructions carefully to ensure the correct proportions and quantities of each media type.
- Housing Reassembly: Carefully position the housing back onto the manifold, ensuring proper alignment and seating. Gently turn the housing to ensure the O-rings on the center and shell tubes are properly seated.
- Yoke and Thumbscrew Replacement: Reattach the yoke and tighten the thumbscrew finger-tight. Avoid over-tightening, as this could damage the plastic shell.
Additional Maintenance Considerations
- Regular Inspection: Regularly inspect the scrubber for any signs of wear, corrosion, or leaks. Promptly address any issues to maintain optimal performance and prevent potential breakdowns.
- pH Monitoring: For scrubbers utilizing aqueous solutions, monitor the pH level regularly to ensure it remains within the recommended range. Maintaining optimal pH ensures effective ammonia removal and prevents potential damage to the scrubber components.
- Pump Maintenance: If the scrubber incorporates a pump, maintain it according to the manufacturer’s recommendations to ensure continuous and efficient operation. Regular lubrication, cleaning, and inspection help extend pump lifespan and minimize downtime.
- Recordkeeping: Maintain detailed records of maintenance activities, including media replacement dates, pH measurements, and any repairs or adjustments performed. This documentation helps track scrubber performance and facilitates informed decision-making regarding future maintenance schedules.
Future Trends in Ammonia Scrubbing
The realm of ammonia scrubbing is undergoing a dynamic transformation, driven by the relentless pursuit of efficiency, environmental sustainability, and regulatory compliance. As technological advancements reshape the industry landscape, novel ammonia scrubbing solutions are emerging, promising to redefine the standard for emission control.
Emerging Technologies
- Membrane Technology: Membrane-based ammonia scrubbers are gaining traction due to their high efficiency, compact design, and reduced environmental footprint. These systems utilize specially engineered membranes to selectively remove ammonia from gas streams, offering a promising alternative to traditional scrubbing methods.
- Advanced Sorbents: The development of advanced sorbents with enhanced ammonia capture capabilities is revolutionizing ammonia scrubbing. These sorbents, often derived from novel materials, exhibit superior adsorption properties, leading to increased removal efficiency and reduced energy consumption.
- Photocatalytic Ammonia Removal: Photocatalysis, the utilization of light energy to drive chemical reactions, is emerging as a promising approach for ammonia removal. Photocatalytic ammonia scrubbers harness the power of light to decompose ammonia molecules, offering a clean and efficient alternative to traditional scrubbing methods.
Regulatory Drivers
- Stringent Emissions Standards: The tightening of emissions regulations worldwide is driving the development of more efficient and environmentally friendly ammonia scrubbing technologies. Scrubber manufacturers are responding by innovating and refining their designs to meet increasingly stringent regulatory requirements.
- Promotion of Sustainable Practices: The growing emphasis on sustainable industrial practices is fueling the demand for ammonia scrubbing solutions that minimize environmental impact. This includes the development of scrubbing technologies that utilize renewable energy sources, reduce waste generation, and promote resource conservation.
- Harmonization of Global Regulations: Efforts to harmonize emissions regulations across different regions are creating a demand for versatile ammonia scrubbing solutions that can adapt to varying regulatory requirements. Scrubber manufacturers are responding by developing adaptable technologies that can meet the diverse needs of industries worldwide.
Conclusion
Ammonia scrubbers play a vital role in emission control, protecting the environment and industrial equipment. By removing ammonia from gas streams, they ensure compliance with regulations, reduce maintenance costs, and safeguard downstream analyzers. As industries seek efficient and environmentally friendly solutions, ammonia scrubbers remain a cornerstone of emission control and environmental stewardship.
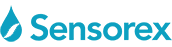
Posted by Joshua Samp on October 23, 2023
Sensorex is a global leader in the design and manufacture of quality sensors for water quality and process applications. The company offers more than 2000 sensor packages for pH, ORP, conductivity, dissolved oxygen, free chlorine, chlorine dioxide, UV transmittance and other specialty measurements, as well as a full line of sensor accessories and transmitters. Its expert technical support engineers solve analytical sensor challenges with custom designs and off the shelf products.